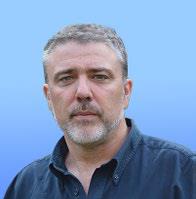
我们很少有机会可以自由发挥。几乎在所有情况下,都必须要在狭小的空间内放入我们的设备。如果想占用已有20年之久的一条电镀生产线所占面积,那么整合最佳新技术所面临的挑战就是要解决空间不足的问题。更甚的是,在解决空间问题的同时客户还要求要提高产能。 而且,埋孔、盲孔和电镀填充导通孔在PCB设计中越来越普及。盲孔和埋孔意味着不同内层连接的数量是多少,电镀设备的负载量就增加了多少倍。采用相同技术意味着设备需要处理越来越薄的材料。镀铜导通孔填充意味着镀槽一定要设计得更大,所以与传统通孔的生产周期相比,镀槽占据的宝贵空间也就越大,生产周期也就越长。一般情况下,通孔电镀需要45分钟至60分钟,而导通孔的孔电镀则需长达3小时至4小时。 众所周知,欧洲的PCB工厂规模通常比亚洲的工厂小很多。这一般意味着欧洲工厂只有一条电镀生产线,而用于这台关键电镀设备一定要能够承接所有产品。所以采用折衷方案是不可避免的,设备通常需要在极端条件下运行。例如,很难使用顶部夹取的方法传送厚重的面板(面板可能会突然从夹具中掉落)。非常薄的面板在浸入镀槽时需要额外的支撑力才不会出现褶皱,也需要支撑力把面板固定在阳极正中心(电镀过程中,靠近阳极一侧会太厚,而离阳极较远的一侧则会太薄)。这两个问题很容易解决,但在两种极端情况同时出现时,则无法采用同一种夹具装置。 解决方案与发展成果 解决分布问题的一种好方法就是将阳极分区。传统可溶性阳极使用填满铜球的钛篮,但这种方法无法控制电镀窗口的不同区域。材料通常会悬挂在单个阳极杆上,电镀电流会被均匀分布至整个阳极区域。使用不溶性铱网阳极将阳极区域分区,通过把阳极分为几个区域来深控制电流分布深度,只在那些前面放置了面板的阳极区域接通电流。所以不需要用浮动保护罩就能更精准地电镀不同长度的面板。 图1:分区后的阳极区域 因为使用了多个整流器,所以能把电镀窗口按整个宽度分为不同区域。通过这种方式,刮板只需要装载部分材料,所以更容易预测电镀效果。这种方法可以和分区阳极一起使用,从而以各种组合方式将电镀窗口分为不同区域,实现更精确的电镀。与分区阳极法一样,这种方法也可以让电镀窗口的使用方式更加灵活。这种采用大量小型整流器的方法可以让垂直连续电镀(VCP)更加适合小批量面板的电镀,让更多小型工厂有机会使用这类设备。 图2:带有多个整流器的阳极杆 VCP的应用越来越广泛,而且可为常见的电镀难题提供多种解决方案。开发这类设备的主要推动因素是行业需要实现整个面板电镀的均匀性。产品在动力驱动下匀速通过镀槽,面板的每个部分都会经过每个阳极,所以从理论上讲,面板的每个部分都会经历完全相同的电流密度高点和低点。VCP工艺并不能称之为新技术,因为这种机器已经出现很多年了,但在各种流程中应用VCP工艺确实是最近开发的。 电镀薄面板时需要涉及到“浸入”工艺,所以这种操作本身有难度。如果使用传统电镀生产线,一定要用夹具支撑面板才能让容易弯曲的面板在浸入镀槽时固定在正确位置。相比之下,VCP可以在特氟龙导轨的帮助下入料,薄材料在通过镀槽的整个过程中都被精确固定在正确位置。即使只采用顶部夹取的方式也可以传送0.05 mm厚的材料。 为了更精确地VCP电镀薄材料,行业开发出了一种同时夹取面板顶部和底部的系统。这种方法的理念是将材料固定在前后阳极之间的正中央。 图3:顶部和底部的VCP夹具 图4:顶部和底部的VCP夹具 电镀用化学药水也是展现新发展成果的领域。最有趣的一点就是人们不得不去考虑“工厂内只有一条生产线”的状况。当你打算开发新技术时,你必须要根据电镀槽中使用的铜溶液来设计实验。我看过一种测试是使用脉冲电镀溶液进行超低区域图形电镀测试(就是在一块空白面板上电镀少量圆形焊盘)。这个测试的有趣之处在于,凭借着简单计算和猜测就得到了良好的效果。最初测试的化学药水是专为反向脉冲电镀而设计的,尽管我们尝试的是完全直流周期。仅凭借一次测试很难去量化化学药水在其中起到的作用,所以很久之后当我们使用传统直流电镀溶液来完成测试时,才意识到最初测试使用的化学药水可能有很大的潜在优势。 总结
Marc Ladle是Viking Test Ltd公司主管。阅读往期专栏或联系Ladle,可点击此处。
更多内容请点击在线查看。