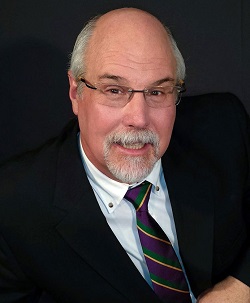
最近I-Connect007编辑团队采访了John Vaughan和Kelly Dack,探讨了部件可获得信息如何以意想不到的方式影响设计团队。Dack首先简述了EMS工厂几乎每天都会发生的真实情况。在采访的这一环节,Dack详细介绍了如何就部件可获取问题与OEM设计团队沟通重新开始设计。
Barry Matties:Kelly,你一直从事设计工作,在设计过程开始时,你可能熟悉制造商,也可能不认识制造商。这两种情况的明显差异是什么?
Kelly Dack:差异在于沟通的层次不同,尤其指的是书面文件的沟通。
目前供应链严重短缺,芯片不再随手可获得,对于EMS行业,迫使我们不得因为更换芯片进行大量的重新设计。原先围绕扁平封装已使用了5~8年的PCB设计不能使用,唯一的替代品可能是0.5毫米间距的BGA。通常,外部设计师会将新的0.5毫米间距BGA集成到现有设计中,在布线技术中采用不同的线宽线距。
设计师将现有0.006”宽的走线缩小到3.5mil,以扇出BGA的I/O。从屏幕上看没问题,一切似乎都可以实现。然而,多年来一直在制造这种PCB的制造商不具备3.5mil线宽的印刷、蚀刻和外层电镀能力。现在怎么办?这就是问题所在。设计师说:“我们的任何裸板样品供应商都能做到。”确实如此。然而,目前的海外批量供应商做不到。
这就需要沟通。我们必须找出可行的解决方案,解决设计师和制造工厂之间的沟通脱节问题。有几种方法可以实现。设计师是否可以使用焊盘内导通孔或HDI技术来向外扇出0.56mm间距BGA的I/O?供应商可以满足这些调整,但无法使用相同的叠层实现外层3mil的线宽/线距。1盎司的基铜太厚了。
在设计发布用于生产并经历更改后,存在很多沟通脱节的环节。沟通是从一开始就决定项目成功的唯一途径。换言之,如果设计师能够利用PCB供应商制造工艺能力,就可以选择适当的叠层和布线解决方案。相反,由于设计师选择未事先沟通选择的布线方式,将迫使EMS供应商采购有可行材料厚度的PCB,因而使整个项目的成本、报价和时间增加。
John Vaughan:在我看来,尽早调整至关重要,这样就不会通过采购推动决策过程。如果设计师尽早与PCB制造商合作,问题就容易解决。
Dack:是的。
Matties:那能节省多少时间?
Dack:重点是产品需要快速上市;时间至关重要。因此,当我们发现某个芯片已经淘汰,或者采购不到时,就是在耗用项目的上市时间。通常,在生产阶段可能需要1到2周的时间才能收到所有报价,并取得新部件可获得性的承诺。如果实施这样的变更需要4到6周以上的时间,也就不足为奇了。
Matties:代价太大了。
Johnson:然而,在我们的行业中,这种情况比以往任何时候都更普遍,所有这些元件的交付周期都延长了。设计师必须管控、重新设计,甚至完全重新配置他们的供应商列表,以提交新版的设计。有太多的内容需要沟通。
Vaughan:你说得对,这是另一个沟通的机会。交付周期很重要,尤其是元件市场,因为按照设计的常规节奏,设计师通常在开始之前就处于紧张状态,常常会落后于项目进度。我相信Kelly可以证明这一点。如果设计阶段结束时再查看所需元件的物料清单,会看到交付周期为20周的元件。在我看来,如果设计师预先考虑了所有物料的可获得性,那么就不必被迫做出一些复杂的决策。
Dack:说得好。
Matties:如果突然无法采购到某个元件或者你必须匆匆忙忙地做一些事情,这就意味着很难确定最后的结果是好还是坏?
Dack:是的。这是一个时间转换过程。一切从标准开始,设计时就要通过标准达到产品规格目标。设计应该做什么?如何实施设计?布局开始之前就要在前端捕捉到这些信息,现在我们转向设计标准,并将这一理念塑造到可以根据产品性能等级在任何地方布局和制造的产品内。当按照设计生产样品时,这是排除任何潜在设计或工程类问题的第一阶段。然后,一旦与样品生产相关的问题得到解决,就会自然地进入批量生产阶段。在这一点上,供应商管理层和潜在供应商之间关于订购特定产品的沟通需要继续加强。
现在,Barry,你提到的观点开始起作用了。我们重新开始。一旦某些元件已被淘汰,就需要再回到设计阶段进行更改。我们是按标准设计的,但现在,突然,标准无法使用,物料清单发生了变化,潜在的替代产品也发生了变化。我们该怎么办?现在,必须从另一方面进行沟通。PCB将在哪里生产?已确定制造商了吗?我们确实想要把它交给那个制造商生产吗?此时,供应商管理层可以将包括设计师在内的所有人聚集在一起,解决已淘汰部件问题。我想这就是解决问题的方法。设计师要了解供应商的能力,将供应商作为解决问题的起点。
Matties:是否可以谈谈数字孪生、自动化或AI工厂4.0是如何影响这一点的?因为有了数字孪生,你必须在把设计发送给制造商或EMS之前解决所有这些问题,在电脑中构建解决方案。这种目标会很快实现吗?
Vaughan:随着新技术的出现,无论是CFX还是其他平台,我们都看到了所有的连接,以及IoT和数字孪生对话正在获得需求的牵引。这一目标即将实现。
I-Connect007编辑团队的结论:
在产品的整个生命周期中对其进行修订是正常的。传统上,这些重新设计被认为是由于部件报废和寿命终止公告导致的,这些公告通常会提前发布。然而,仔细思考一下,部件寿命终止只是一种特殊情况,扩展到临时可获得性问题可能需要做出相同的响应,但行业几乎没有收到任何警告。
Kelly介绍的实例清晰地表明了这种相似性:交付周期现在是导致PCBA重新设计以采用新的不同部件,从而保持生产可继续进行的关键因素。PCB需要重新设计以适应新的芯片,同时,还可能触发紧固件或软件的重新设计,以适应元件功能变化。
随着变化的深度逐渐显现,简单更新所涉及的范围和工作都在滚雪球般扩大,所涉及的沟通量可能会令人望而生畏。
EMS团队很快会意识到这个问题。只要能采购到经认证为与装配/外形/功能兼容的替代部件,问题就很简单,但实现这一目标并不容易。在最近与Screaming Circuits公司的Duane Benson(I-Connect007专栏作家)的一次对话中,他指出,即使在同一产品线的部件中(例如,同一系列中的Arduino微控制器上有不同数量的RAM),封装也可能有大不相同的I/O引脚。换句话说,即使是简单的升级到同一控制器的更高RAM版本,也会触发PCB的重新设计。
这使EMS公司成为问题的最初负责人,需要与制造工厂和OEM设计团队进行沟通,需要寻找具有决策权的适当负责人。
然而,OEM设计团队也预料不到像这样的重新设计,因此在部门的项目进度表中没有计划,就要开始有效利用资源,开始与EMS沟通。
当展望数字孪生的未来,其获取设计意图和设计数据本身的新兴能力时,我们期望看到这种动态沟通的逐步改进。