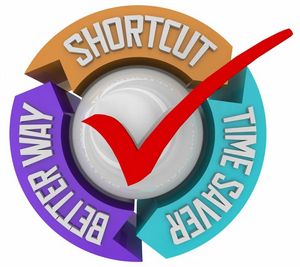
感谢Haley Fu博士在本文翻译过程中给与的支持。
摘要
三防漆的目的是保护PCB及安装在PCB上的元件免受湿气、颗粒物和腐蚀性气体的侵蚀。测试三防漆有效性的传统方法是将涂有三防漆的组件暴露在腐蚀性环境然后确定平均失效时间,整个周期长达数月。本文将介绍一种耗时不到一周的快速测试方法。
在该测试方法中,采用暴露于硫黄气体环境中的铜和银薄膜腐蚀速率来表征三防漆的性能。本文简述了测试箱的设计和配置,研究了温度和湿度对铜和银薄膜腐蚀速率的影响,得出丙烯酸酯、硅酮和原子层沉积(ALD)三防漆的性能,以及不同温度和相对湿度条件下它们的表现。采用的测试温度为40℃和50℃,温度会影响三防漆下铜和银薄膜的腐蚀速率。测试的相对湿度为15%、31%和75%,相对湿度对腐蚀速率的影响较小。笔者详细讨论了3种三防漆在防腐表现上的显著差异,并建议了测试的最佳条件。
引言
三防漆的目的是保护PCB及安装其上的元件免受湿气、颗粒物和腐蚀性气体的损害。腐蚀性环境可能含有高浓度的气体,如二氧化硫、硫化氢、游离硫、氯、氮氧化物和臭氧。当空气中的相对湿度高于颗粒物的相对湿度时,具有低潮解相对湿度(deliquescent relative humidity,简称DRH)的颗粒物可以通过形成低电阻桥(电气短路)而使具有电位差的特征电气短路。随着数据中心类设备被应用到高污染和相对湿度高的地区,三防漆的使用变得非常有必要,特别是对于关键的设备和可靠性要求高的军事领域[1-5]。元件特征尺寸减小也促使三防漆成为必要。随着特征间隙的减小,灰尘颗粒和腐蚀产物颗粒更容易造成桥接短路,因此三防漆在设计中需要慎重考虑和选择。
市场上有各价格档次的易于涂覆的三防漆,可有效保护底层金属免受腐蚀。评估三防漆的行业标准方法是将其涂敷于实际应用的硬件上,确定其平均失效时间。这种测试方法很不方便,且效率低,例如对于表面贴装电阻器,在温度、湿度和环境腐蚀性非常有限的条件下,评估涂层有可能需要一年多的时间[5-7]。
评估的一种便捷方法是在铜和银上薄膜上涂覆三防漆,在腐蚀和潮湿环境下监测所涂覆三防漆的腐蚀速率[8-9]。本文详细介绍了所提出的表征三防漆特性的测试方法。测试方法评估了在4种不同温度、湿度条件下的3种不同涂层(丙烯酸、硅酮和ALD)。采用了修改版的iNEMI硫华试验箱(flowers of sulfur,简称FoS)[10-13]。
实验步骤和结果
用于评估三防漆的试件是在15mmx15mm的氧化硅晶片上喷镀一层800nm厚铜的或银的蛇形薄膜结构,晶片黏在PCB样板上。把带4个L形引脚的连接件的一端焊接到PCB上,另一端用银环氧树脂连接到蛇形薄膜的4点接触焊盘上。银环氧树脂需要在流动氮气和140℃下烘1小时。氮气保护层避免了金属薄膜的氧化。L形引脚的另一端焊接到PCB的可插接连接器。图1是蛇形薄膜试件的横截面示意图及实物照片。
图1:a)蛇形薄膜试件结构,在早期研究工作中,使用底部薄膜来加热顶部薄膜;b) 在本文所述的试验中未使用底部薄膜
使用待测试的三防漆涂覆薄膜试件。把直径为50微米的T型热电偶细线黏在蛇形薄膜试件三防漆上面。把试件安置悬挂在改造过的iNEMI 硫华试验箱FoS的侧壁[10-13],并通过适当的引线连接到恒电位仪(见图2)。对原始硫华试验箱所做的改变是移除了旋转装置和盛放漂白剂的器皿。因此,试验箱内没有强制空气流动,也没有氯气。箱内的腐蚀性气体只有硫黄蒸气。当箱内温度为40°C时,硫黄浓度为0.15×10-6,当箱内温度为50°C时,硫黄浓度为0.3 ×10-6[14]。使用ZnCl2饱和盐溶液可将箱内相对湿度控制在15%,使用MgCl2饱和盐溶液可将相对湿度控制在31%,或使用NaCl饱和盐溶液将相对湿度控制在75%。箱内空气没有像在之前的爬行腐蚀测试项目中那样强制循环[10-13] 。
a)FoS硫华试验箱的内部;
b)盛有硫黄和饱和盐的托盘;
c)试验装置总览
图2:安装了薄膜试件的FoS硫华试验箱
使用恒电位仪可控制通过薄膜试件的电流,通过测量电压可观测到薄膜电阻的变化。使用连接到数据记录仪的热电偶监测薄膜温度。在测试期间(5.32天),电阻和温度值每10分钟读取一次。
项目测试了3种三防漆:厚度为39~45μm的丙烯酸涂层、厚度为100μm的硅酮涂层、厚度为0.1μm的ALD涂层。ALD具有涂层超薄(1~200nm)、化学计量、致密、厚度非常均匀的特点。ALD工艺在真空反应器中进行,温度相对较低,通常为80~300°C,取决于所涂覆的材料和基板的导热性。为了表征/评估三防漆,我们把有三防漆涂层的薄膜腐蚀速率和未经涂覆的(裸)薄膜的腐蚀速率进行了比较。
图3:4种温湿度测试条件
如图3的温湿度表所示,测试箱采用了4个不同的温湿度条件进行测试:(1)相对湿度为15%、温度为40℃;(2) 相对湿度为15%、温度为50℃;(3)相对湿度为31%、温度为50℃;(4)相对湿度为75%、温度为50℃。如前所述,使用饱和盐溶液控制测试箱内的湿度。表1列出了不同电流和温度条件下的测试持续时间。
表1:40°C下FoS腔的电气和温度测试条件
测试包括在不同温度下的测试周期。尽管希望是在每段测试时间内保持温度恒定,但随着时间推移,薄膜电阻的升高会造成薄膜温度相应升高。如公式(1)所示,通过计算薄膜冷却到一定温度To时的电阻值来补偿温度的影响。
温度补偿(校正)电阻R(t,To)可用以下关系式来计算薄膜厚度:
铜和银薄膜电阻的温度系数的测定如图4所示。腐蚀产物的高电阻率让我们可以忽略腐蚀产物平行电阻路径的影响。
图4:确定电阻温度系数值的方法
测试箱的温度决定了硫蒸汽的浓度,而通过选择不同的饱和盐溶液则决定了测试箱内的相对湿度。另外,通过分析铜箔和银箔的腐蚀产物可间接测定试验箱内空气成分的腐蚀性。铜箔和银箔经由试验箱前门上的窄槽插入到试验箱内,暴露在试验环境中,通常为一天。采用库仑还原法可测定每天腐蚀产物的总厚度[15]。铜箔、银箔每天的腐蚀速率如图5所示。可以看到室温影响明显:40℃条件下腐蚀速率小于50℃时的腐蚀速率;另一方面,相对湿度较高时,腐蚀速率较低。在较高湿度下,水雾表面吸附了硫蒸气,从而降低了测试箱内的硫浓度。较低的硫浓度使空气腐蚀性降低。
图5:FoS试验箱中a)铜箔和b)银箔的腐蚀速率
如前所述,我们测定了涂有三防漆的铜和银薄膜的腐蚀速率。测试的涂层为丙烯酸、硅酮和ALD。硅酮涂层对其下薄膜的保护最小;而ALD涂层提供了最佳保护。图6至图10比较了这两种涂层覆盖的铜薄膜和裸铜薄膜的测试结果。图6提供了在5.32天的测试期间样品的温度分布数据。图7是采用4点测量法和用恒电位仪所得到的薄膜未校正电阻值。图6和图7中的数据提供了确定薄膜电阻率温度系数所需的充足信息。从这些图中,可以获得图8所示的温度补偿(校正)电阻曲线。从图8中,我们可以计算铜随时间变化的腐蚀速率,如图9所示。铜腐蚀指的是由于腐蚀而造成的铜厚度的减少,而图5的腐蚀速率是指生长在铜箔上的腐蚀产物的总厚度。生长在铜箔上的铜腐蚀产物的总厚度是因腐蚀损失的铜厚度的2倍。从图9中的曲线斜率,我们可以得出铜腐蚀速率随温度的变化,并按图10所示的阿伦尼乌斯(Arrhenius)方式绘制。ALD涂层下的铜及银薄膜的腐蚀速率非常低,在实验误差范围内,在图9中测量不到,也就无法在图10中表示出。
图11总结了裸(未涂覆)铜和裸银薄膜的腐蚀速率以及涂覆有丙烯酸或硅酮的薄膜腐蚀速率。由于涂覆有原子级沉积(ALD)涂层的薄膜腐蚀速率在实验误差范围内,因此未包括其腐蚀速率。
图6:40℃和15%相对湿度下,FoS硫华试验箱中铜薄膜温度随时间的变化
图7:40°C和15%相对湿度下FoS腔中不同薄膜温度下铜薄膜的未修正电阻、时间的函数。标称薄膜温度为42°C时,持续0~1.85天;温度为52℃时,持续1.85天~3天;温度为64°C时,持续3天~4.16天,温度为42°C时:持续4.16天~5.32天
图8:温度为40℃和相对湿度为15%条件下,FoS箱中铜薄膜的校正电阻随时间的变化。第0~1.85天薄膜在名义温度42℃条件下进行测试;第1.85天~3天测试温度为52℃;第3~4.16天测试温度为64℃时,第4.16天~5.32天测试温度为42℃。
图9:温度为40℃和相对湿度为15%条件下,FoS箱中铜薄膜腐蚀程度随时间的变化。第0~1.85天薄膜测试的名义温度为42℃;第1.85~3天测试温度为52℃ ;第3~4.16天温度为64℃;第4.16~5.32天温度为42℃。
图10:温度为40℃和相对湿度为15%条件下,FoS腔中铜薄膜腐蚀速率的阿伦尼乌斯图
图11:裸铜和裸银薄膜以及涂有丙烯酸或有机硅的薄膜的腐蚀速率总结。ALD涂层薄膜的腐蚀速率不包括在这些曲线图中,因为其腐蚀速率太低,在实验误差范围内。
讨论
图11总结了涂覆有丙烯酸或硅酮的铜和银蛇形薄膜的腐蚀速率,并将其与裸铜薄膜和裸银(未涂布三防漆的)薄膜的腐蚀速率进行了比较。ALD涂层薄膜因腐蚀速率太低以致量测不到,故未包括在内。
丙烯酸涂层在一定程度上保护了铜薄膜免受腐蚀。在40℃的FoS环境下,涂覆有丙烯酸涂层的铜腐蚀速率比裸铜低2个数量级。将FoS环境温度提高到50℃会使涂覆有丙烯酸涂层的铜薄膜腐蚀速率增加大约1个数量级。在3种湿度测试条件(15%、31%和75%)中,相对湿度为75%时,涂覆有丙烯酸的铜腐蚀速率最高。丙烯酸涂层不能保护其下的银薄膜。把温度从40℃升高到50℃确实在一定程度上增加了银腐蚀速率。
硅酮涂层对其下的铜薄膜没有防腐保护作用。在温度为40℃和相对湿度为15%条件下,硅涂层对银薄膜具有一定的防腐作用。温度为50℃时,在测试的所有相对湿度条件下,硅涂层对银薄膜没有防腐蚀保护作用。
图12:温度为50°C和相对湿度为31%的条件下,进行5.32天测试后蛇形薄膜的图片
图12给出了底层金属腐蚀程度的外观定性证据,与图11中绘制的金属腐蚀速率一致。ALD涂层明显为底层铜薄膜和银薄膜提供了极佳的防腐蚀保护。丙烯酸涂层可保护铜薄膜,但不能保护银薄膜,与图11一致。硅不能保护铜薄膜或银薄膜,与图11一致。另一个有趣的观察结果是:这3种三防漆均可阻止裸露的银薄膜上Ag2S晶须的生长。
预估产品实际使用可能发生的失效通常需要进行加速试验,包括采用更高的温度和更恶劣的环境,以缩短测试时间。严苛条件的弊端是,可能会对硬件施加过大的应力,从而改变实际现场发生失效的机理。更好的方法是保持测试条件与现场条件接近或相同,并通过提高检测硬件退化的灵敏度来缩短测试时间。本文采用了后一种方法,在通过表征三防漆的基础上,对有涂层的薄膜腐蚀速率的测量灵敏度可低至±1nm。因此,无需加速测试条件。本项研究和早期的研究表明,40℃FoS硫华试验箱中的环境条件足以测试三防漆[8-9]。在本项研究中,对测试箱内的空气没有机械性搅动。今后我们将继续研究温和机械搅动空气对测试的影响。
结论
本研究再次证明使用铜薄膜和银薄膜可以评估三防漆的防腐效果。考虑到温度对薄膜电阻的影响,采用四点测量法可以非常有效、准确地测量金属薄膜的腐蚀速率。薄膜温度必须用细丝连接热电偶进行测量。温度修正后的薄膜电阻与剩余的膜厚成反比。剩余膜层厚度的下降速率正是薄膜的腐蚀速率,可用于表征三防漆所提供的腐蚀防护。使用改造的iNEMI 硫华试验箱,在40℃的测试环境条件下足以进行三防漆测试。不采用过度试验条件的优点是,测试中的退化失效机理与产品使用现场中的机理相同。
参考内容
1.ASHRAE white paper, Particulate and Gaseous Contamination in Datacom Environments, 2nd Edition, ASHRAE, Atlanta, GA, USA.
2.R. Danilak, “Why energy is big and rapidly growing problem for data centers,” https:/www.forbes.com, 15Dec 2017.
3.Airside economizers and ASHRAE standard 90.1-2013, Trane Engineers Newsletter, vol 44-2.
4.O. V. Geet, “A method for estimating potential energy ad cost savings for cooling existing data centers,” NREL, https://www.nrel.gov/docs/fy17osti/68218.pdf.
5.Cole M., L. Hedlund, G. Hutt, T. Kiraly, L. Klein, S. Nickel, P. Singh, T. Tofil, “Harsh Environment Impact on Resistor Corrosion,” SMTA International Proceedings, 2010
6.Lembke P., M. Cole, T. Tofil1, J. Porter, J. Wertz, J. Wilcox, M. Gaynes, M. Meilunas and H. Rubin, “Testing and Mitigating Silver Sulfide Corrosion,” SMTA International, Rosemont, IL, Oct 2018.
7.Cole M., J. Porter, J. Wertz, M. Coq, M. Meilunas, J. Wilcox, “Effectiveness of Conformal Coatings In Preventing Resistor Silver Sulfide Corrosion,” SMTA International, Rosemont, IL, Sept 2016.
8.Singh P., Characterization of conformal coatings, SMTA International, San Diego, Feb 2015.
9.Singh P., “Conformal Coating Characterization Using Stacked Thin Films,” 2020 Pan Pacific Microelectronics Symposium .10-13 Feb 2020.
10.Singh P., L. Palmer, Fu H., D. Lee, J. Lee, K. Guo, J. Liu, S. Lee. G. Tong, C. Xu, “Round Robin Evaluation of the iNEMI Creep Corrosion Qualification Test,” IPC 2018 APEX EXPO, 28 Feb to 1 Mar 2018, San Diego, CA, USA.
11.Singh P., L. Palmer, Fu H., D. Lee, J. Lee, K. Guo, J. Liu, S. Lee. G. Tong, C. Xu, “Round Robin Evaluation of the iNEMI Creep Corrosion Qualification Test,” IPC 2018 APEX EXPO, 28 Feb to 1 Mar 2018, San Diego, CA, USA.
12.Singh P., M. Fabry, W. B. Green, “Flowers of sulfur creep corrosion testing of populated circuit boards,” Proc. IPC APEX EXPO, San Diego, CA, 1316 Feb 2017.
13.Singh P., M. Cole, T. Kiraly, J. Tan, R. Rangaraj, G. Wood, T. Chang, “Comparing Flowers of Sulfur and Mixed Flowing Gas Creep Corrosion Testing of Printed Circuit Boards,” SMTA Int’l, Rosemont, IL, Sept 2016.
14.Hindin B,. Private communication, Battelle Memorial Laboratory, Columbus, Ohio, USA.
15.Krumbein S.J., “Monitoring Environmental Tests by Coulometric Reduction of Metallic Control Coupons,” J. of Testing and Evaluation, 17(6), 357-367, 1989.
Prabjit Singh是IBM的资深技术专家,主要领域是冶金和材料工程及微电子制造。
本文作者如下 Prabjit Singh and Larry Palmer, IBM Corporation;
Chen Xu, Jason Keeping, Marko Pudas;
Mei Ming Khaw, Kok Lieh Tan, Keysight;
Mike Huang, Ruby Lin, Wistron Corporation;
Haley Fu, iNEMI
欢迎扫码关注我们的微信公众号
“PCB007中文线上杂志”
点击这里即可获取完整杂志内容。