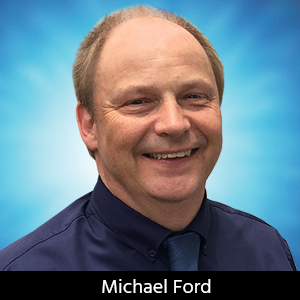
Henry Ford在他所处的时代引发了一场工业革命;批量生产的效率实现了常见产品的快速生产,使得人人都可享用。然而这种意识形态的制造方法已经发展到了不再可行的程度。针对高效制造技术,目前的好消息是出现了新一代技术。
回顾批量生产
从批量生产到灵活批量生产配置的演变是建立在有缺陷的前提下。当时的目的是,每一辆黑色的T型车都机械地从生产线上下来,每一辆车都代表着立即售出。批量生产原则要求总装生产线连续运行,不可因任何原因停止。只要供应网络中有持续的需求、足够的质量和准时交付,生产就能很好地运行。然而这种做法导致一系列以“做业务”为幌子的妥协,成为批量生产业务模式中被接受和不受欢迎的组成部分。
对于批量生产,销售组织一直面临着保持需求平稳流动的压力。大型OEM公司发现,他们可以将广告活动费用与客户需求影响联系起来。这只是做业务的成本。不幸的是,竞争对手使用了同样的工具,扰乱了精心设计的需求模式,导致了对另一种市场营销工具的需求,使另一种业务成本的效果大打折扣。当然竞争对手也在做同样的事情,均形成了螺旋式、成本驱动的销售策略。
由于这种策略在盈利方面是不可持续的,设计师们面临创建独特而引人注目技术的压力,这些技术可以用来将新产品与竞争对手区分开来。随着产品变得更小、更轻、能耗更低、更智能,具有讽刺意味的是,产品也同时变得更大、更重、更耗电,新技术的竞争成本高企(但也有新闻价值)。随着技术创新成本变得过于高而难以维持,对互操作性和技术通用化的需求极大地削弱了这种方法。
因此,在许多情况下,批量生产原则本身受到了威胁。本应持续运行的生产线被停止,因为分销网络中超额库存成本的重要性已包含在总成本计算中。组装生产线上的产品转换更加必要,因此增加了产品品种,减少了批量数量。同样这需要付出高昂的隐性成本。不仅关键设备在大部分时间里没有增加价值,这是大多数公司在企业管理中隐藏的事实,而且具有讽刺意味的是,需要更多的货物库存来应对批量生产,并满足来自分销网络日益不稳定的需求。
汽车行业无法在这样的条件下生存,而是选择建造批量生产线,至少在一定程度上,这些生产线具有应对总组装生产线变化的能力。汽车量产生产线的最终成果现在看起来与最初的T型车生产线大不相同,因为现在有多种颜色和型号,以及性能、舒适度和宽松的选择。复杂的排序系统以外科手术的精密度管理每个单独产品的创建。仅仅一条连续的生产线就可以支持数百万种不同的产品组合。
权衡是什么?
这种灵活性导致了巨大且大多是隐藏的成本。尽管最终的生产线运行顺利,但变化带来的痛苦和成本却传递给了上游的供应商,制造商的需求变化很大,同时需要完美的质量和及时交付。反过来,供应商与他们的供应商也有困难,因为不能准确预测对物料或元器件的需求。与其他行业相比,供应网络问题和风险增加很快变得极具破坏性,正如我们看到的疫情后供应网络问题。
这种问题积累的另一个现象,特别是在汽车行业(甚至在疫情之前),是从下订单到交付的交付周期。有时甚至要半年才能完成订单,这让许多客户望而却步。与此同时,更多基本的“填充”规范被插入到计划中,以保持生产线的运行,这些规范可以通过经销商或在线第三方销售。我们看到了奇怪的库存持有方法,未售出的汽车被闲置在空地,因为它们需要大幅折扣才能售出。
这些成本和损失意味着极大的浪费。Henry Ford批量生产的经济性之所以奏效,是因为他是第一个这样做的人。这种特有浪费的演变使该行业走向了下一次工业革命,工业4.0。对大多数制造业来说,它仍然是令人困惑的技术。一定程度上是因为工业4.0让我们倒退,而不是前进。在Henry之前,产品都是定制的,根据客户的要求量身定做。对于大部分制造业来说,市场要么已经恢复到这种状态,要么正在恢复。不管我们喜欢与否,一次性文化正在被一种基于价值和可持续发展的文化所取代。因此,制造业必须拿出新的方案来应对这一早已存在的挑战。
我们拥有Henry时代所没有的先进技术。从硬件的角度来看,自动化现在具有很强的适应性,并且基于其编程,能够处理各种需求。这样的程序数据以及手动组装的说明可以针对每个生产批次进行定制。只需读取传入的生产单元ID,就可以提供适当的安装和组装指令,甚至可以为每个单独的产品定制。现代MES的作用是确保每个操作的个性化都得到自动管理和执行,且可全面了解进度和物料管理。
对许多公司来说,本能是回避这一原则。例如,尽管精益生产已证明在匹配批量生产的有效水平方面取得了成功,但由于大多数制造应用的工作站和操作员培训的复杂性,它被认为过于极端。现有技术已经成为一种观念,即现实世界的制造既得不到批量生产衍生模型的支持,也得不到精益生产的支持。这两种方法都代表了企业必须妥协的理想。
销售、市场营销和分销网络对业务的积极贡献始终胜过制造车间的优先事项,而制造业一直被认为是制造产品的引擎。公司发现很难投资制造业,在许多情况下,他们很高兴看到将制造的责任交给地球另一端的第三方。但这并不是应用最先进技术的最佳方法。
现代方法
可组合制造是更现代的方法。可组合制造不是对抗和抵制客户需求模式,而是拥抱它们。在数字化的推动下,它达到了批量生产和精益生产之间的最佳点。可组合性允许准确地根据需要在有能力的生产站之间自由分配工作,包括大批量、多品种批次,甚至是单独定制的产品。可组合的工作指令直接来源于设计数据,遵循组合的用户界面和设备程序模板。基于以产品为中心的数据模型,可以快速轻松地选择最佳生产配置,没有工程设计负担。操作员和设备都只需遵循一组单独的任务。在执行过程中,连续收集可追溯信息,对每个完成的步骤进行确认,确保不会出现错误或遗漏。
可追溯性信息,以来自手动和自动操作的数据收集的形式,在内部及时的基础上构成工作分配和物料的流程和分布,实现可见性和控制。自适应规划可确保整个制造组件和最终产品层次完全满足发运要求,无需库存多余的成品,并且几乎消除了交付延迟的风险。这是推动工业4.0的核心原则,可组合制造精密而独特地解决了这一问题。
基于可组合性的工厂可以在任何需要的时候,以任意数量和配置高效地生产任何产品。这种生产模式对企业的潜在影响是巨大的。销售和市场营销不再因为需要出售滞留在分销链上的近乎过时的过剩产品而受到影响。工厂可以在整个产品生命周期中利用竞争对手的弱点,以更快地引入新的或更新的技术。
可组合制造使制造回到目标市场,消除了分销链中隐藏的多种浪费。对于需要通过消除分销成本浪费同时保持敏捷和高效来接近客户的行业来说,可组合性是自然的选择。
现代MES解决方案并不是简单地自动化已经存在的一切。它不仅仅是收集数据并让客户决定如何使用。现代MES推动了最佳的新制造实践,可满足不断发展的客户需求模式要求,并强调质量、可用性、价值和性价比,而不是生产具有环境挑战性、最便宜和可丢弃的产品。组合制造既适用于目前的工厂,也适用于未来工厂。
更多内容可点击这里查看,文章发表于《PCB007中国线上杂志》23年11月号,更多精彩原创内容,欢迎关注“PCB007中文线上杂志”公众号。