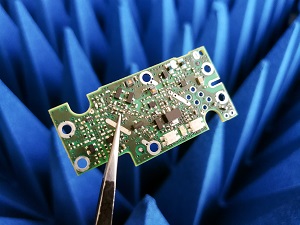
为了了解测试及检测的最前沿观点,I-Connect007编辑团队采访了总部位于圣地亚哥的VAS Engineering公司制造工程师Raj Vora和运营经理Darren Carlson,该公司一直非常关注运营效率。他们认为“条条大路通罗马”,因此,似乎任何提高运营效率的工作最终都会归向数据和分析。在此次采访中,Raj和Darren分享了测试及检测设备对整个制造结构效率的重要性。
Nolan Johnson:当贵公司考虑整体企业运营时,测试和检测的重要性如何,你们认为检测存在什么挑战?
Raj Vora:检测是我们生存的烦恼之源,它对整个运营至关重要。我们对所有3条生产线上的每块PCB进行在线AOI。如果有任何附加工作,例如机箱机柜的机械装配,我们也会进行100%的最终人工检测。
其中的挑战之一是SMT工艺中的一些设备出现错误报警。我们正试图通过更换所有的检测设备来缓解这一问题。
Barry Matties:当你们在审查设备时,采取什么策略?你们如何看待会影响今天所做决定的未来?
Vora:我们想解决的一大难题是MES软件。实时反馈是关键。假设我们正在运行一项作业;参考指示符会触发一些缺陷条件,希望就在这个环节,MES相关的实时软件能够在开始犯更多错误之前锁定生产线并纠正错误。我们很快就会去解决问题,已经在进行MES软件的询价(Request For Quotation,简称RFQ)流程。
我们有很多好的软件,但其中大部分数据并没有整理成为好的一组数据,这是面临的一大问题。第二个问题是我们想要更好的车间控制,所以已经将库存数字化。现在,公司的库存管理系统就像数据库,这是巨大的质量改进。
现在,我们正在追求质量,以及为了全面了解这个系统,关注所有联系在一起的数据。质量可能有很多不同的组成部分。我们已经建立了一些定制的内部软件,希望成为先进的工厂。
我们不做焊膏(SPI)或回流焊前检测,因为还没有发现对其的需求。回流焊后数据表明我们的工艺状况良好,这源于高水平的持续维护和内部员工的知识水平。几乎95%的设备维护都是由公司的内部员工完成的。
Matties:对于贵公司的SPI,即将推出的更精细特征会导致你们改变策略吗?
Vora:数据会告诉我们该怎么做。我们已经在生产有01005元器件的PCB了。例如,我们有一块板,它有25个行项目,就是在一枚硬币大小的PCB上,共有185个贴装点,其中01005有40~50个贴装点。
Matties:是用钢板印刷焊膏还是喷射打印焊膏?
Vora:用钢板印刷。在这种情况下,钢板涉及很多技术。虽然钢板通常只需200美元,但这块钢板成本高达1000美元,其中有一些技巧。通过这块钢板我们已取得了巨大成功。
Matties:贵公司也在考虑采用喷射打印焊膏工艺吗?
Vora:没有必要投资喷射打印工艺,因为我们希望能够在3条生产线上的任何一条线上运行任何作业。钢板印刷已经做得很好了,我们真的是一家批量生产厂,有时间制作钢板。附近还有一个钢板生产厂,如果有需要,他们可以在当天交付钢板。
Matties:在线AOI是贵公司获得实时反馈以控制制程的关键点吗?
Darren Carlson:是的。现在,我们正在利用操作员控制制程。运行AOI的人会标记生产线,而不是由软件数据采集系统标记。它是半自动的;仍存在大量操作员干预。
Vora:我们仔细查看这些数据,以了解缺陷率和成因。缺陷的原因是什么?有多少缺陷?例如,为什么会突然出现墓碑缺陷?
Matties:那么,贵公司是在利用这些数据进行实时过程控制和改进吗?
Vora:MES软件将把所有这些数据整合在一起,并显示在一些大屏幕上,以实现极端的实时反馈。这就是我们收集制程中每个数据的目的。
Johnson:贵公司是否期望MES软件标记并停止生产线,而不是依靠操作员来完成?
Vora:没错。如果每百万个机会突然出现低于99.9%的缺陷部件,可以相信一些控制输送带的小装置,让我们实时锁定输送带。我们不确定有多希望自动控制生产,因为那样就会带来一大堆问题。我认为过程缓慢,所以将根据具体情况而定。
Matties:客户对测试有什么要求?
Vora:AOI检测对一些客户来说是必须的。一些客户要求进行成品电气测试。当我们检测首块PCB时,有些客户想出现在现场。通常,我们的大生产客户有一些要求,但他们非常放手。每当出现问题,我们都会打电话给他们,他们会很快做出反应。
Matties:贵公司生产挠性电路还是刚挠结合PCB?
Vora:我们正在做很多样板。我们做了一些批量PCB;大多数批量PCB都是刚挠结合PCB,这意味着我们将部件大多放置在刚性表面上,但也有挠性部分。
Matties:测试和检测过程如何因应用而异?
Vora:仍然通过AOI决定。如果PCB上面有任何贯穿孔,仍然会进入最终检测环节。我们尽可能保留拼板,可以更容易地对其进行返工和检测。
Carlson:如果需要的话,我们会制作托盘,或者使用其他方法使其在贴装过程中更加稳定。
Matties:随着UHDI技术及更精细特征的增多,对贵公司的测试和检测过程有什么影响?
Carlson:开始稍微突破我们的能力范围了。
Vora:这样很好,因为这迫使我们更快地发展。早些时候,他们开始使用01005,正因为如此,我们最终购买了新设备,到目前为止效果良好。
Matties:UHDI看起来将成为一项更常见的工作。你们所收获的经验将如何帮助你走向未来?
Carlson:最重要的是让设备能够处理这些技术。我想有些买不起新一代设备的公司可能无法完成这类生产。
Matties:贵公司升级设备后,会处于有优势。
Vora:在公司的发展历程中,现在正处于引人注目的位置。大约3年前,我们开始专注于数字化,并真正了解工艺流程。一旦我们将库存管理数字化,就启动了工厂的新一代变革。现在我们正处于成长阶段,已经确定了60%的流程,并将继续开展这项工作。
Johnson:你刚才提到在数字化库存管理中发现了很多好处。公司正在积极考虑变革检测。您能否量化或描述数字化如何提高贵公司的盈利能力?
Vora:让我们看看AOI。我们需要有人坐在设备前吗?还是这可能是一种“区域”而不是“人对人”的防御?当我们能够做出这些改变时,我们就会看到改进。实际上,我们的目标是找出如何放置更多部件。目标是整体设备效能(Overall Equipment Effectiveness,简称OEE)。
我们如何在OEE方面获得最高效的运营?当生产线放置部件时,我们会产生收入。每一次机器坏了,我们就停止盈利。这就是为什么我们的目标是围绕OEE。但是,如果我们生产线效率很高,却有大量的返工,那就不是我们想要的。
这就是AOI将在实时工厂意识中发挥作用的地方,这样在设备仍在放置部件时,电路板就不需返工。
我们首先要确保物料数量非常准确,这样设备就可以随时放置部件。现在我们已经完成了这项工作,让AOI和MES真正成为参与者,让我们实时了解生产线的表现。在不返工的情况下,我们能以多快的速度将其上线和下线?
Johnson:你做来料检测吗?
Vora:没有那么多检测。我们非常信任我们的授权供应商。他们很少寄来物料包装内有错误部件的未标记的NPN。
Carlson:这几乎是零,可能10年内有几次。
Vora:对首次使用的PCB进行检测,通常会检测裸PCB。当从授权供应商那里购买时,一切都没问题。
Matties:提到测试及检测,你最关心的是什么?
Vora:当首块PCB没有通过第一次测试时,是可怕的时刻。最怕是贴装了错误的0201,那么每块PCB就百分百放错了一个0201元器件,因为这个电阻器看起来和另一个电阻器完全一样。这些都是我们所担心的,而不是它是否能通过测试。
首件PCB 很重要。我们真的把PCB上的每个部件都捡起来,用一些智能镊子测量,然后把它放回PCB。我们测量每一个参考标示符。我们做了初始AMI来匹配所有的出版说明和所有的案例标记。首件检测是我们非常重视的环节,甚至在那之前,我们的来料站(IMS),一张玻璃桌面下面内置了相机,为每一个进入公司的物料卷拍照;我们将物料卷上的元数据记录到数据库。我们正在努力主动确保当它被放在PCB上时不会出现错误放置问题。
Johnson:这正是贵公司数字工厂的起点。
Vora:没错。任何物料一进入公司都是如何处理的?它是如何被贴上标签的?贴标签后是否进行验证?即使在我们正在研究的软件中,也有测量部件的过程,然后才能通过系统中的唯一ID获得批准。
Carlson:我们对AOI的恐惧之一是虚假的逃逸;我们认为一切都很好,但涉及到客户的环节时,就出现了问题。
Vora:有时候客户的BOM是错误的。我们将AOI和整个流程编程到BOM环节;确保文档正确可以避免错误。
Matties:检测从数据层面开始。
Vora:使用目前的软件,每个客户有内部部件号;所有部件都按客户分开放置,不再共享部件。这是我们为了更好地管理库存而做出的决定。
我们构建了在BOM引入期间使用的软件;将BOM与原系统中已有的所有部件进行对比,并主动进行匹配。每次现有客户引入BOM时,只有10%~30%的零件是新的。我们做了很多前期工作。
我们创建了一些不同的软件来帮助早期进入阶段。这种方法很有帮助,因为可以以更快的速度完成这项工作,并增加质量保证。
Johnson:当VAS这样的公司必须编写自己的软件时,通常是因为供应商的软件存在功能差距,迫使你们推出自己的软件。你们发现软件存在哪些漏洞?
Vora:我们通过MES搜索发现,想要的功能大约85%是可能实现的。诚然,这不是最初认为的目标;世界比我们现在发现的要先进得多。并不是说我们很智慧,但我们认为他们已经找到了答案。
我们发现每个公司做事方式都不一样。制造公司没有标准的运营方式,无论是在设备、工艺流程还是使用的软件方面;没有解决方案是完美的。
现在大多数软件都带有可用的API。我们没有建立定制的高端软件,而是从ERP购买了API。我们没有构建自己的数据库,而是在数据之上增强数据和应用。这就是我们发现很多价值的地方。
当我们在ERP中完成管理流程时,我们发现更多无法解决的流程缺口。我认为ERP真的不是为EMS行业构建的。目前有几款ERP软件,其中一款在解决电子制造服务的ERP困境方面做得很巧妙。这就是差距的地方。我们在制造方面存在差距,但些差距可以通过现有的MES软件平台来解决。
Matties:所以,真正给所有这些优化带来动力的是数字工厂和基准化流程。这就是目前如何最大限度地利用检测的方法。
Vora:是的,工作流程自动化。让工作在公司中流动,而不是我们每次都要接触所有的工作。我们正朝着这个方向前进,最终,我们可以添加机器人过程自动化(Robotic Process Automation ,简称RPA)。现在,我们的目标是工作流自动化:工件是如何找到下一个人的,而不是人找到下一个工件?
Matties:现在,当对流程进行基准化时,有什么惊喜吗?
Vora:我们学到的第一点是,当设备没有贴放部件时,我们就赚不到钱,我们的设施也无法正常运行。现在,我们在检查工厂的运作方式时,会积极考虑这一应对措施。我们的主要目标是实现这部分操作的自动化。
高价设备就是高成本。虽然Darren多年来一直在提到它,但我大约在一年半前就开始明白和理解它。我正在构建可以计算的对数计算器,随着时间的推移,它可以计算我们应该如何引用某人的话。就在那时,我看到了它:“如果我们不贴装部件,我们就不能赢利,因为这就是费用,不管怎样,只要开门运营,就要支出3万美元。”
令我大开眼界的是,建立自动计算器来引用人工。就在那时,我们开始了基准测试,意识到我们可以很快做出改变,因为已经解决了库存管理的主要问题,包括未知的短缺、仓库中的物料位置、已知的好物料等。真正好的数据将帮助实现这些目标。在获取数据并利用它的过程中,我们发现了价值,因为现在数据可以说话。在做了平均成本分析后,每一点改进都有助于公司保持增长。
Matties:我认为,基准测试会收紧公司的流程窗口,从而提高公司的能力。
Vora:当然。Darren正在用轮换做一些有趣的事情。我们了解到,当我们的一名高技能操作员作为系统转换专家而不是操作员工作时,我们会看到改进。不需要他站在生产线前,而是作为流动人员。我们想,让他做公司的系统转换人员。
Matties:这是否改变了你对员工的整体看法以及他们发挥作用的方式?你说让员工提升技能,找到员工的真正价值,员工是公司拥有的最大资产。
Vora:它每天都在慢慢地改变我们的观点。
Carlson:我们已经朝着多任务员工的方向发展。尽管可能会雇佣他们为SMT操作员,但我们正在努力寻找具备可以随时前往任何其他制程工序的多种工作技能的员工。
Johnson:是否可以介绍贵公司选择新设备的流程?
Vora:我们精于参考设备用户的意见。我们建立表格并发送给设备用户。填写表格大约需要10分钟。表格列出了典型的问题,使我们能够专注于真正重要的问题。
其中很大一部分问题是用户对设备安装的评分,可从1到5给出评分。如何评价设备供应商的支持(从1到5)?如果我们发现推荐公司总是说支持可给5分,我们就不需要问了;我们知道他们会说什么。然后,在沟通中强调我们最需要了解的设备信息。
我们现在正在关注两个不同的制造商;其中一家制造商把我们和一家公司联系起来,这家公司过去和我们有同样的设备。我们进行了非常愉快的对话。我们询问了他们转而采用新AOI设备的前3大原因,我们发现他们也遇到了 和我们相同的问题。这台设备为他们解决了这些问题:错误报警、良好的数据、良好的SPC软件。但让人更高兴的是,他们已经与我们正在考虑的几个MES合作伙伴整合在一起了。这是我们看中的重点。
我们总是询问推荐者是否要操作员一直坐在AOI设备前。这个新设备是否不再需要操作员,这一点很重要,因为这意味着他们相信设备能完成工作。
他们是否相信AOI设备正在实现其应有的价值?现在,我们正在寻找两个具有不同技术的供应商来阐释电路板数据。其中一个供应商在如何进行AOI方面有一种独特的方法——基于激光加2D。在检测时,哪种技术能提供更好的结果?
Carlson:公司目前面临的最大挑战是自己造成的。我们的3条生产线有4台AOI,都出自同一家供应商,但每台AOI设备都有不同的视场相机,其中2个有不同的软件。我们正在寻找生产线之间的连续性;设备之间共享同一个程序的标准化。我们更多地着眼于大局,着眼于长期,以达到下一个高度。
Johnson:贵公司面临的挑战是什么?
Vora:元器件尺寸是重点。我不想一直这么说,但一切的重点都是数据。这个系统能在多大程度上集成,使数据更有意识和价值,从而指导所有这些不同的部分和决策?
计划和调度是非常困难的任务,要能够在正确的日期正确的时间生产PCB。比如发现计划表上的另外两块PCB有很多共同的元器件,只是交付时间不同,为什么不把它们放在一起生产呢?我认为这就是人工智能将发挥作用的地方。然而,要做到这一点,需要有可用的数据,这样“主机”才能做出决策。为了理解工厂意识,可以将多少数据流拼接在一起,下一步用这些数据可以做什么?
通过购买全新的AOI解决方案,我们已经在考虑未来5年的发展。我们正在寻找最先进的3D系统技术,以应对线宽线距低至7微米的PCB。这就是为什么我们要在同一天在所有生产线上使用相同的全新设备。
在Darren看来,一旦开始标准化,我们就可以更快地开始下一步的努力,为更快的增长打下坚实的基础。
Johnson:贵公司是否认为检测设备的软件扩展性对你们来说非常重要?并不是说相机的硬件或细节,而是将其集成到目前系统并扩展它们的能力。
Vora:是的,把这一切集成在一起是关键。需要提及的一点是编程速度。我们正在关注的两家公司有两个新的人工智能引擎,可以帮助加快编程速度。过去需要两个小时,现在只需要30分钟。人工智能是热点,已经出现了一些好的使用案例。
Matties:对于那些正在探究测试策略的公司,你们有什么建议吗?
Vora:公司的测试部门正在完成一项自动化项目。我相信很多大公司都已经这样做了,但我们是多品种、小 批量的生产企业,要实现自动化更加困难。我们正在完成自动化工作,公司有一位擅长CAD的自动化工程师。我们正在生产固定装置,用弹簧销将其连接到6轴机器人上。再将那些弹簧销连接到计算机上。我们正在自动化编程和测试,因为公司每天都要做很多编程测试。这是我们真正关注的工作。挑战在于如何在多品种、小批量的环境中实现编程测试。